KHS ist ein weltweit tätiger Spezialist für Getränkeabfüll- und Verpackungsanlagen. Das Werk Dortmund beliefert die KHS Gruppe weltweit mit Ersatz- und Neuteilen. Die mechanische Fertigung in Dortmund ist dabei für Einzelteile und Kleinserien mit geringer Wiederholhäufigkeit zuständig. Dazu zählen auch Teile für Umbauten, die in der Regel schnell verfügbar sein müssen. Gefertigt wird an rund 60 Werkzeugmaschinen und zehn Bearbeitungszentren. Aufgrund der Teilevielfalt und dem hohen Variantenreichtum beansprucht das Umrüsten der Maschinen enorm viel Zeit. Zeit, die man wegen der begrenzten Maschinenkapazitäten aber nicht hat. Eine effiziente Werkzeugorganisation kann hier einiges bewirken, wie sich bei KHS zeigt.
Vor vier Jahren noch dominierte eine dezentrale Werkzeugbevorratung die Ersatzteilfertigung in Dortmund: Einzelne Werkzeuglager befanden sich in unmittelbarer Nähe der zehn Bearbeitungszentren. Lediglich schneidende Komponenten und Montagewerkzeuge sowie Mess- und Prüfmittel lagen in einer zentralen Werkzeugausgabe des Werkzeugvoreinstellraums. Das Wissen über den Zusammenbau der Komplettwerkzeuge besaßen Maschinenbediener und Einrichter. Jeder baute „seine“ Komplettwerkzeuge in unterschiedlichsten Varianten zusammen. Auch war die Bezeichnung alles andere als eindeutig. „Es kursierten bei uns für ein und dasselbe Werkzeug oft mehrere Bezeichnungen, was bei 8300 Einzelkomponenten und 3700 Komplettwerkzeugen der Transparenz kaum dienlich ist“, erinnert sich Matthias Boldt. Dieser sorgt als Leiter Werkzeugmanagement mit seinem Team dafür, dass möglichst keine Maschinenstillstände durch fehlende Werkzeuge entstehen.
TDM als Basis für den gesamten Werkzeugkreislauf
Um Ordnung in die Bestände zu bekommen und mehr Transparenz zu schaffen, begann KHS deshalb mit dem Aufbau einer Werkzeugdatenbank zur zentralen Verwaltung von Werkzeugkomponenten, Komplettwerkzeugen, Mess- und Prüf- sowie Spannmitteln und Vorrichtungen. Durch die verbesserte Transparenz in der Fertigung sollten sich Werkzeugbestände und die Werkzeugvielfalt reduzieren sowie Fehlbestände der Werkzeugkomponenten vermieden werden. Zugleich wollte man Rüstzeiten minimieren und damit die Produktivität an den Werkzeugmaschinen steigern. „Gerade bei der Einzelteilefertigung von Ersatzteilen ist es wichtig, die Maschinen optimal auszulasten“, betont Matthias Boldt. „Wir haben mit der TDM-Software die Basis für ein durchgängig integriertes Toolmanagementsystem gelegt.“ Der komplette Werkzeugkreislauf ist heute in TDM abgebildet, sämtliche Werkzeug- und Technologiedaten sind erfasst und für die NC-Programmierung und Werkzeugbereitstellung aktuell abrufbar. „Mit TDM haben wir eine komplett neue Systemlandschaft und Organisationsstruktur aufgebaut.“
Sichere Fertigungsprozesse durch Simulation
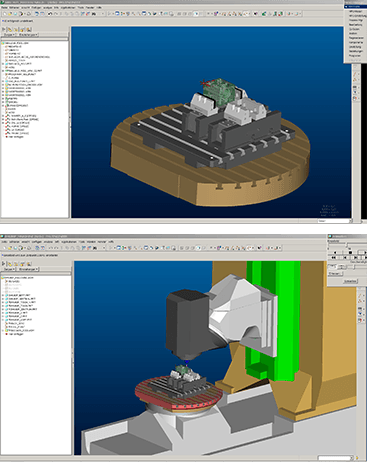
Durch den Zugriff auf die Werkzeugdaten ließ sich zudem die NC-Programmerstellung optimieren. Die Bereitstellung von Geometrie- und Technologiedaten und 2D- und 3D-Werkzeuggrafiken ermöglicht eine realistische Simulation der Bearbeitung an der Maschine. Bedingt durch die Vielzahl an unterschiedlichen Einzelteilen, die auf den Maschinen gefertigt werden, war man sich nie ganz sicher, ob ein NC-Programm hundert Prozent stimmt. „Früher mussten wir uns vorsichtig an jeden Bearbeitungsprozess herantasten, um Kollisionen auf den Bearbeitungszentren auszuschließen“, erinnert Matthias Boldt. „In TDM haben wir teilweise mehrere Technologiedatensätze zu jedem Komplettwerkzeug hinterlegt. Damit wird der gesamte Einfahrprozess nicht nur sicherer, sondern auch erheblich beschleunigt.“
Aufbauend auf TDM hat KHS das CAD/CAM-System Pro/NC für die NC-Programmierung eingeführt: „Mit der Entscheidung für TDM als unternehmensweite Software für Werkzeugdatenverwaltung haben wir das alte CAM-System durch Pro/NC abgelöst und an TDM angebunden“, erklärt Matthias Boldt. Der Toolmanager und sein Team konnten so parallel zwei strategische Projekte realisieren: Eine Schnittstelle oder genauer gesagt eine Online-Integration von TDM in Pro/NC sorgt heute für den direkten Zugriff auf Werkzeugdaten von TDM aus dem NC-Umfeld. Es ist kein Systemwechsel mehr erforderlich für die Auswahl und das Laden von Werkzeugdaten. In Pro/NC lassen sich die erstellten NC-Programme bereits vor dem Post Processing-Durchlauf simulieren; Störkanten werden frühzeitig erkannt. Die endgültige Werkzeugliste für ein getestetes NC-Programm wird in TDM abgespeichert und ist für die Werkzeugmontage, die Voreinstellung am Zoller-Voreinstellgerät sowie die Maschineneinrichter mit den entsprechenden Daten und Informationen verfügbar.
Was aber nützt die Fertigungssimulation ohne entsprechende Daten von Spannmittel und Vorrichtungen? Diese werden mit der TDM Werkzeugplanung und PDMLink gepflegt und sind so auch für die Planungs- und Simulationsabläufe verfügbar. Damit wird die gesamte Aufspannsituation an der Maschine virtuell sichtbar und simulierbar. „Jedes Komplettwerkzeug, das heute gezeichnet wird, lässt sich problemlos zusammenbauen“, weiß Matthias Boldt. Der Grund: Die verwendete Aufnahme ist auf jeden Fall vorhanden und befindet sich nicht im Maschineneinsatz. Durch das nahtlose Zusammenspiel aller eingebundenen Systeme ist das vollkommen transparent.
Einen wesentlichen Vorteil bringt die Verwendung des TDM Daten- und Grafikgenerators mit sich. Dieser erzeugt aus hinterlegten Katalogwerkzeugen verschiedener Hersteller quasi auf Knopfdruck simulationsfähige 2D- und 3D-Grafiken. Die fertigungsnahe Simulation half der Fertigungsplanung bei KHS dabei, vom „gewohnten“ Testen an den Maschinen wegzukommen und dadurch kostbare Maschinenstunden zu sparen. „Durch die tiefe Integration von TDM und Pro/NC sehen wir sofort, ob sich beispielsweise ein Werkzeug tatsächlich so zusammenbauen lässt, wie es gezeichnet ist, ob die Verfahrwege stimmen oder Kollisionsgefahr besteht – samt der ebenfalls in TDM angelegten Spannmittel und Aufnahmen.“ (Zur Zeit in Planung: Ist das NC-Programm soweit „sicher“, soll nach dem PP-Durchlauf in Vericut realitätsgetreu die Maschinensimulation durchgeführt werden.) Einen Unsicherheitsfaktor konnte Matthias Boldt trotz TDM nicht ausschließen: das Flattern bei labiler Aufspannung. „Vibrationen sieht man eben in der Simulation nicht.“ Die Maschinenbediener aber wissen aus Erfahrung, dass insbesondere bei langen Auskragungen unerwartet Vibrationen auftreten können und fahren deshalb langsamer ein.
Geordnete Werkzeuglagerung: transparent und aktuell

Damit der Werkzeugkreislauf vom Lager über die Voreinstellung an die Maschine und zurück ins Lager funktioniert, kommt überall TDM zum Einsatz. Die Philosophie ist so einfach wie effektiv: Kommen die Werkzeuge zurück von den Maschinen, werden sie je nach Verschleiß und Verfügbarkeit komplett oder demontiert eingebucht. (Anhand der Angaben der NC-Programmierer über Mindestschneidenlänge und Mindestgesamtlänge wählt der Werkzeugeinrichter ein geeignetes Werkzeug, bevorzugt nachgeschliffen, aus. Danach richtet er es ein und bucht es auf die jeweilige Maschine.) Die Shuttles werden ebenfalls mit dem TDM Lagermodul verwaltet sowie angesteuert. Sämtliche Werkzeugbewegungen werden auf Kostenstellen gebucht, was ein transparentes Werkzeugcontrolling ermöglicht. Die Werkzeugbeschaffung erfolgt über die SAP-Schnittstelle: Via Buchungsdaten wird der Werkzeugbedarf an SAP weitergegeben. Für die Übergabe der Informationen sind die SAP-Warensachnummern in TDM hinterlegt. Die Anbindung von TDM an SAP besteht schon viele Jahre und erleichtert den Beschaffungsprozess von Werkzeugen enorm.
Auf der Basis von TDM findet jetzt eine Standardisierung im gesamten Werkzeugbereich statt. „Ohne das Lagermodul wäre dies nicht möglich gewesen“, so Boldt. Hinterlegt sind die Werkzeugdaten der Hersteller, und auch die jeweilige korrekte Bezeichnung ist nun einheitlich nach deren Standardbezeichnungen eingepflegt. Beispiel: Tieflochbohrer anstelle von Langbohrer oder Tiefbohrer für ein und dasselbe Werkzeug – so erzeugten die Mitarbeiter früher immer wieder Dubletten. Und auch die Beschaffungsphilosophie hat sich inzwischen geändert: Bohrer, Fräser und Co. sollen möglichst immer vom gleichen Hersteller stammen, um die Datenerfassung in TDM zu erleichtern. „Immer dann, wenn ein Werkzeug eines anderen Herstellers nicht mehr lieferbar ist oder sich der Schneidstoff ändert, bestellen wir dies dann neu bei unserem Standardlieferanten“, erläutert der Leiter Werkzeugmanagement. Und: Diese Vorgehensweise bringt zugleich auch Kostenvorteile bei Bestellungen mit sich. Zudem ermöglicht das TDM Mess- und Prüfmittelmodul eine effiziente Überwachung aller vorhandenen Mess- und Prüfmittel. Besteht solch ein Werkzeugverwaltungssystem in allen Werken, lassen sich nicht benötigte Werkzeuge sowie Mess- und Prüfmittel von einem Standort an einen anderen weitergeben und damit ebenfalls Anschaffungskosten senken. Zurzeit wird das Modul über vier Werke hinweg, die bereits TDM einsetzen, mandantenübergreifend genutzt.
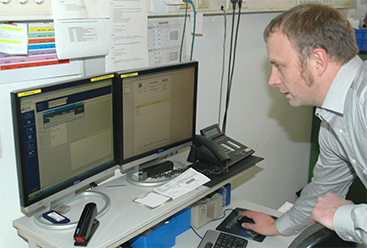
Alle zehn Bearbeitungszentren in Dortmund sind inzwischen auf TDM umgestellt, die Werkzeugausgabe erfolgt zentral an einer Stelle. In zwei Kardex-Shuttles auf 15.500 Lagerplätzen liegen geordnet sämtliche Werkzeugkomponenten, Komplettwerkzeuge, Spannmittel, Vorrichtungen sowie Mess- und Prüfmittel: in Summe 8.300 Einzelkomponenten, 11.500 Mess- und Prüfmittel und 3700 Komplettwerkzeuge. Gebucht wird auf 930 Kostenstellen und Arbeitsplätzen. Sämtliche nicht mehr benötigten Werkzeuge wandern meist demontiert sofort zurück ins geordnete Lager, für jeden auffind- und abrufbar.
Ein Bohrer T10 ist jetzt nicht mehr in 15 Varianten erfasst, sondern einmal, eindeutig klassifiziert und für jeden auf Knopfdruck auffindbar. „In TDM sehen wir sofort, welche Werkzeuge in welcher Anzahl vorhanden sind, welche sich in den Maschinenmagazinen befinden, welche im Lager“, ist Matthias Boldt von der hohen Auskunftsbereitschaft der datenbankbasierten Werkzeugverwaltungssoftware überzeugt. Mehr noch: Verwendet gerade ein Kollege an seiner Maschine ein teures Sonderwerkzeug, wird dies auf Anhieb ersichtlich – Doppelbestellungen teurer Komponenten entfallen somit, die Kosten für die Werkzeugbeschaffung reduzieren sich.
Und auch die Kommunikation hat sich deutlich verbessert. Geht die Werkzeugliste an die Einrichter, geben diese ihre Erfahrungswerte jetzt in TDM ein, so dass die NC-Programmierer wissen, was an den Maschinen läuft. Umgekehrt vertrauen die Maschinenbediener heute den zuvor simulierten NC-Programmen. „Wir ziehen alle an einem Strang und der heißt TDM“, sagt Boldt.
KHS – das Unternehmen
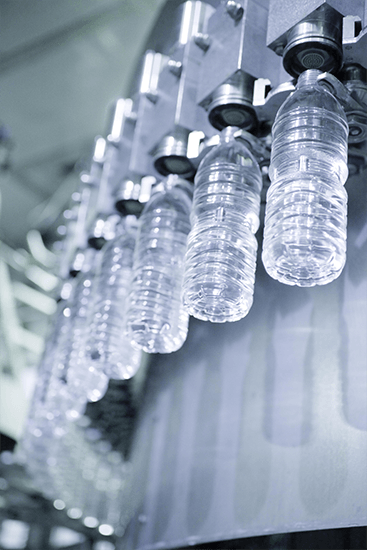
Die KHS GmbH, Dortmund – international tätiger Hersteller von Abfüll- und Verpackungsanlagen für die Getränke-, Food- und Nonfood-Branche – ist 1993 aus einem Zusammenschluss der 1868 gegründeten Holstein & Kappert AG, Dortmund, und der 1887 gegründeten Seitz-Werke GmbH, später SEN AG, Bad Kreuznach, entstanden. Das Unternehmen ist eine 100%ige Tochtergesellschaft der Salzgitter Klöckner-Werke GmbH, die zum Salzgitter-Konzern gehört.
Der zentral von Dortmund aus geführte KHS-Konzern realisiert heute mit ca. 4.500 Mitarbeitern weltweit einen Umsatz von über 900 Mio. Euro.
KHS hält eine führende Stellung im Bereich der Abfüll- und Verpackungstechnik innerhalb der Getränkebranche. Jüngste Entwicklungen wie innovative Trockenteil-Lösungen in Modulbauweise, universelle Füllsysteme, Hochleistungs-Etikettiertechnik, modernste Kommunikations- und Diagnosetechniken u. v. a. m. dokumentieren die Marktposition als Innovator.