KHS operates worldwide as a specialist for filling and packaging systems for drinks. The Dortmund plant supplies the KHS Group globally with replacement parts and new parts. In this process, the mechanical production department in Dortmund is responsible for components and small production series with a low repetition frequency. This also includes parts for reconstructions which must usually be quickly available. Parts are manufactured on around 60 machine tools and ten machining centers. Due to the multiplicity of parts and extremely wide range of variants, retooling the machines demands an enormous amount of time. Time which one doesn’t have, because of limited machine capacities. Efficient tool organization can be beneficial in this respect, as has been shown at KHS.
Four years ago, replacement part manufacturing in Dortmund was still dominated by a decentralized tool crib system. Separate tool cribs were located in the immediate proximity of the ten machining centers. Only cutting components and mounting tools, as well as gauge and calibration equipment, were held in a central tool crib of the tool presetting room. Only machine operators and tool had knowledge about the assembling of tools. Everybody assembled “his” tools in highly diverse/ different variants. Also tool designation was far from clear. “At our works, several different designations were often in circulation for the very same tool, which hardly aids transparency when you are dealing with 8300 individual components and 3700 tools”, recalls Matthias Boldt, who, as Head of Tool Management, together with his team endeavors to ensure that, as far as possible, there are no machine downtimes due to missing tools.
TDM as the foundation for the entire tool cycle
To organize the stocks and get more transparency, KHS therefore started to create a tool database for the central management of tool components, tool, gauge and calibration equipment as well as clamping devices and fixtures. By improving transparency in production, the intention was to reduce tool stocks and the number of different tools as well as to avoid stock deficiencies of tool items. At the same time, the desire was to minimize set-up times and consequently increase machine productivity. “Particularly with the individual manufacture of replacement parts, it is important to use the machines to the fullest possible capacity”, stresses Matthias Boldt. With TDM software, we have laid the foundation for a continuously integrated tool management system.” Today, the complete tool cycle is represented in TDM, all tool and technology data is recorded/stored and are available for NC programming and tool provision. “With TDM, we have created a completely new system landscape and organizational structure.”
Reliable production processes through simulation
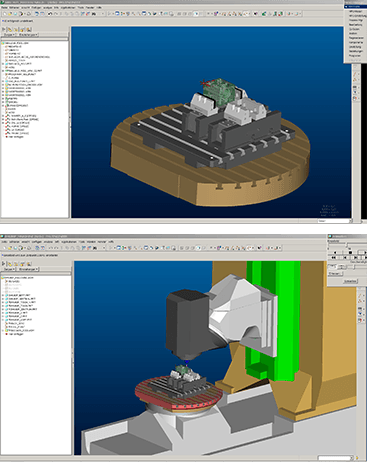
Through access to tool data, NC program creation could besides be optimized. The provision of geometry and technology data, and 2D and 3D tool graphics enabled realistic simulation of the machining process on the machine. Because of the multiplicity of different components which are manufactured on the machines, it was never possible to be completely sure whether an NC program was absolutely correct. “In the past, we had to approach every machining process carefully in order to exclude the possibility of collisions on the machining centers”, recalls Matthias Boldt. “In some cases, we have stored several technology data records for each tool in TDM. As a result, the whole run of process is not only more reliable but also considerably accelerated.”
Building on TDM, KHS has introduced the CAD/CAM system Pro/NC for NC programming. “In deciding for TDM as company-wide software for tool data management, we have replaced the old CAM system with Pro/NC and linked it to TDM”, explains Matthias Boldt. In this way, the tool manager and his team were able to realise two strategic projects: An interface, or more precisely, an online integration of TDM into Pro/NC now provides direct access to TDM tool data from the NC environment. There is no change of system required for selecting and loading tool data now. The created NC programs can be simulated in Pro/NC even before the post-processing. Collision contours are recognized early on. The final tool list for a tested NC program is stored in TDM and is available with the corresponding data and information for tool assembly, presetting on the Zoller presetting and for machine setters.
But what use has production simulation without corresponding information on clamping devices and fixtures? This data is maintained with the TDM tool planning system and PDMLink and is therefore also available for planning and simulation processes. As a result, the whole clamping procedure can be seen and simulated virtually on the machine. “Every tool that is drawn today can be easily assembled”, says Matthias Boldt from experience. The reason: The adaptor used is always available and is not in use on a machine. This is completely transparent due to the seamless interaction between all the systems involved.
The use of the TDM Data and Graphic Generator also provides an essential benefit. From recorded catalogue tools of various manufacturers, it produces 2D and 3D graphics, which can be simulated, virtually at the touch of a button. Simulation, which closely reproduces the manufacturing process, helped production planning at KHS in moving away from the usual practice of performing tests on the machines themselves, and thereby also saving valuable machine hours. “Due to the profound integration of TDM and Pro/NC, we can see immediately whether a tool, for example, can in fact be assembled in the way it has been drawn, and whether the travel lengths are correct or whether there is a risk of collision – together with the clamping devices and adaptors, which have also been created in TDM.” (Currently in planning: When the NC program so far is “reliable”, realistic machine simulation is to be implemented in Vericut following the post-processing cycle.) Matthias Boldt could not rule out an instability factor, despite TDM: wobbling under an unstable clamping. “Vibration is just not seen in the simulation.” Machine operators, however, know from experience that there can be unexpected vibrations, particularly where tool over hangs are involved, and they therefore run in more slowly.
Organized tool storage: transparent and up-to-date

In order that the tool cycle from tool crib via presetting to the machine and back into tool crib operates/works correctly, TDM is used at every stage. The philosophy is as simple as it is effective: When the tools come back from the machines, they are booked into the tool crib either assembled or disassembled, depending on their wear and availability. (Based on the information from the NC programmers about minimum cutting length and minimum total length, the tool setter selects a suitable tool, preferably reground. He then sets the tool and books it on to the respective machine.) The shuttles are also managed and activated with the TDM Tool Crib Module. All tool movements are booked to cost centres, which enables transparent tool controlling. Tools are procured via the SAP interface: Tool requirements are relayed to SAP via booking information. The SAP goods part numbers are stored in TDM for the transfer of the information. The linking of TDM to SAP has been existing for many years and facilitates the tool procurement process enormously.
Based on TDM, a standardisation is now taking place across the entire range of tools. “Without the Tool Crib Module, this would not have been possible”, says Boldt. The tool data of the manufacturers is recorded and the respective correct designation has now also been uniformly entered according to their standard designations. Example: Deep-hole drill instead of long drill or deep drill for the very same tool – so, in the past, workers repeatedly produced duplicates. And procurement philosophy has now also changed: Drills, mills, etc. should, as far as possible, always originate from the same manufacturer in order to facilitate data capture in TDM. “Whenever a tool of another manufacturer can no longer be supplied or the cutting tool material is changed, we always reorder this tool from our standard supplier”, explains the Head of Tool Management. And: At the same time, this procedure also produces cost benefits for orders. Besides the TDM gauge and calibration equipment Module, the MPO, allows efficient monitoring of all existing gauge and calibration equipment. If such a tool management system exists in all factories, tools as well as gauge and calibration equipment which is not required can be passed from one location to another and, thereby, acquisition costs can also be lowered. At present, the module is used across four factories which already implement the TDM system.
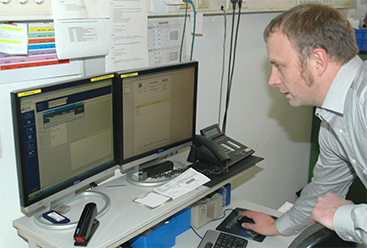
All ten machining centres in Dortmund have now switched over to TDM, with tools issued centrally from one point. All tool items, tool, clamping equipment, fixtures as well as gauge and calibration equipment are orderly arranged and kept in two Kardex Shuttles on 15,500 stock locations: in total 8,300 components, 11,500 items of equipment and 3,700 tools. Booking is made to 930 cost centres and workstations. All tools which are no longer required are mostly disassembled immediately moved back into the orderly arranged tool crib and can be found and accessed by all.
A T10 drill is now no longer recorded in 15 variants but only once. It is clearly classified and can be located by everybody at the touch of a button. “In TDM, we can immediately see which tools are available in which quantity, which ones are located in the machine magazines and which are in the stock”, says Matthias Boldt, convinced of the high level of readiness to supply data provided by the database-supported tool management software. What is more: If a colleague is just using an expensive special tool on his machine, this can instantly be seen and consequently, the double ordering of expensive components is avoided and the costs for tool procurement are reduced.
And communication too has significantly improved. When the tool list goes to the setters, they now enter their experiences into TDM so that the NC programmers know what is running on the machines. Conversely, machine operators now trust the previously simulated NC programs. “We all pull together towards TDM”, says Boldt.
KHS – the commpany
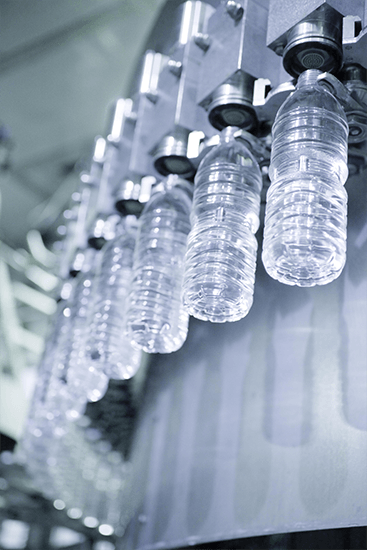
KHS GmbH, Dortmund – internationally operating manufacturer of filling and packaging systems for the drinks, food and non-food sector – was created in 1993 from a merger between Holstein & Kappert AG, Dortmund (founded in 1868) and Seitz-Werke GmbH (founded in 1887), later SEN AG, Bad Kreuznach. The company is a hundred percent subsidiary of Salzgitter Klöckner-Werke GmbH, which is part of the Salzgitter Group.
The KHS Group, which is centrally led from Dortmund, today has around 4,500 employees worldwide and achieves a turnover of more than 900 million euros.
KHS occupies a leading position in filling and packaging technology within the drinks sector. Latest developments, such as innovative dry part solutions of modular construction, universal filling systems, high-performance labelling technology, state-of-the-art communication and diagnostic technologies and many others besides, document their market position as innovator.