With our software for production workflow organization you get perfect transparency at any time!
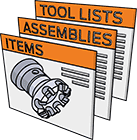
TDM shows which tools are taken from the machine, records the disassembling and storage, archives the NC program, and supports the data transfer from the machine to TDM, and it does so not only during preparation but also after order completion. The entire production workflow is taken care of with TDM.
Managing production equipment made easy
Tool Lifecycle Management is the IT strategy for production equipment. It includes tool organization in all phases of the workflow: from planning to production. The TDM software makes it quick and easy to retrieve tools. It helps assemble the tools correctly and prepare the machines ok. The production equipment management software increases quality and displays the availability of all resources needed for an order. The simplified entry of data significantly increases efficiency and overall performance. Each function of TDM is a building block of a well-functioning Tool Lifecycle Management system within a workflow automation.
By using our software for production workflow you get a further link within the Tool Lifecycle Management
Tool Lifecycle Management is a link between ERP, PLM, and MES. It secures communication between the systems for planning and production. Tool Lifecycle Management captures tool data and graphics and then makes these available in the CAM and simulation processes. It also manages the physical organization of the tool circulation on the shopfloor level. Our TDM software helps you with your process automation and workflow management.
Managing your production equipment with TDM shows clear benefits
The production equipment management solution offers clear benefits. It makes it easier for users to enter data, which in turn facilitates more efficient use of tools. With our software for production workflow management, process automation has never been that easy. Let the benefits speak for themselves: