Along with the 45% reduction in scrap rate because of the wrong holders used or tools being set wrong, Clearwater Engineering, Derby, KS (www.clearwateren.com) had a 26% reduction in tool usage, and realized 350 hours savings in setup as well as other savings since we implemented TDM.
Said Jaramie Cool, Clearwater Engineering (Derby, KS) Engineering Director, “It’s an amazing software. We are glad we invested in TDM. It’s been extremely helpful for both our engineering and the shop floor.”
Clearwater Engineering was a small firm that refused to accept second best. The result for this aircraft component engineering and production specialist: steady growth. “When I began with the firm in 2006, we had five employees,” says Jaramie Cool, Engineering Director at Clearwater Engineering, “today we have forty, with a facility expansion planned within the next two years.”
Information overload
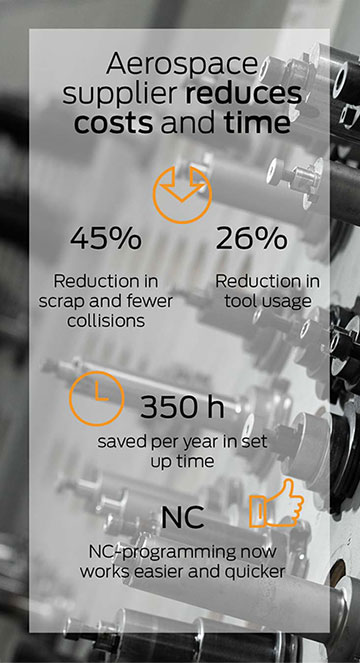
Clearwater deploys an impressive production arsenal to perform its chosen role as a custom manufacturer of complex aerospace parts and precision assemblies. “We have 11 CNC machines,” says Cool, four 3-axis, three 4-axis, and four 5-axis along with numerous other machine tools.
“We use a lot of cutters and have 123 endmills in our library, and 487 items overall, including holders, drill bits, and the like.
“I was heavily involved in our shop floor trying to standardize what we are doing in this respect as we grew,” he continues. “Nobody was quite sure what we had available. We were frequently delayed by getting tools wrong and matching the wrong insert or the wrong holder with the tool. There was too much searching through drawers for the right tool. This resulted in too much and unnecessary custom-made tooling. A similar situation existed with our programs. Finally, we decided there must be a better way.”
In the winter of 2017-18 Cool searched intently online. One possible solution stood out from the rest. “TDM, I liked the fact that they interfaced with CATIA because we rely heavily on it.” Clearwater makes extensive use of the latest CATIA V5 capabilities.
Integration is a large part of TDM’s appeal for Clearwater. “Just as we thought it would, TDM has a lot to offer us,” notes Cool. “Among other things, it can integrate with other systems, such as into our presetter. And it’s expandable, which is a very important feature, because not only can it integrate production and engineering operations but higher-level systems like MRP as well.” “Full implementation,” he adds, “took us about six months. Now we’re 100% TDM.”
TDM’s capabilities in the abstract are impressive, but what has it done so far for Clearwater? It’s a subject that Cool enjoys discussing.
“When a tool is called for, the system prints out a bar code. This leaves no ambiguity as to the correct tool. We’re confident we can precisely match that tool to the right toolholder because our holders now come with numbers from TDM etched into them.”
“We’ve had a 45% reduction in scrap due to wrong holders used or tools being set wrong, all thanks to TDM.” Cool notes.
“The TDM catalog feature and the fact that they have a massive database for tools have been extremely helpful. We can store all of our tool list and have a record of what a particular cutter was used for and import all those tool programs back into our system for future use or reference.”