Coolant seems to run in his veins: Stefan Kempf puts his heart and soul into being the head of contract manufacturer at Norbert Kempf GmbH in St. Ingbert, a town in Saarland, Germany. The company employs approximately 100 employees and manufactures parts and assemblies for customers in the fields of pneumatics, hydraulics, automotive, construction machinery, and prototyping in 2500 square meters of space. Every day, about 2500 parts leave the operation.
Kempf also manufactures machine pallets. For nearly two decades, from 1974 to 1991, the company was involved in special-purpose machining manufacturing, with an in-house design department. And although Kempf has since moved away from this area, it still benefits today from the know how gained, as Stefan Kempf explains: "The experience from that period helps us today in our manufacturing of jigs and fixtures, since we supply our machining centers with their own multiple-part clamping fixtures." These are assembled outside the machines and transported to the machines via robot, so as not to interrupt the machining process any longer than necessary.
Nothing out of the ordinary at first glance. However, a second look would prove worthwhile. Almost all of the machines are in production around the clock; the utilization rate is nearly 100 percent. Nevertheless, there is no hustle and bustle in the halls; everyone is concentrated, but relaxed, in short: The shop runs.
Reliable Processes are essential
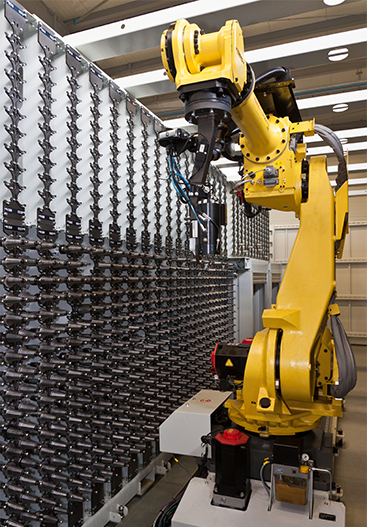
Since 1991, Stefan Kempf has been at the company founded in 1970 by his father, Norbert, in his own home "between the washing machine and the clothesline." He has been the sole managing partner for the last five years and makes no secret of his recipe for success: "Our utilization rates are based on absolutely reliable and reproducible processes that can only be achieved through rational tool management beforehand." The secret behind it all: The TDM Tool Data Management system from TDM Systems GmbH in Tübingen, Germany, ensures the necessary data transparency. From the large selection of TDM software modules for production resource management, shop floor management, data and graphic generation, and interfaces, the Saarland-based Kempf GmbH had TDM Systems assemble a package customized to meet the company's needs.
For years, Kempf and its employees had analyzed the restricted crib again and again in search of the causes of errors. Result: "60 to 70 percent of all errors are caused by mismanagement of tools, assembly errors, poor radial or axial run out, wrong individual items, or because the tool was not getting to the machine on time." Other factors played only a subordinate role. "I can sometimes bring machine pallets and workpieces quickly down the hall to the machine with the forklift, but without tools, my shopfloor comes to a standstill." Since coming to this realization, the three main prerequisites for smooth production are in his mind: The tool, the tool, the tool.
Every new order initiates a process planning order, from the production control plan via the Failure Mode Effects Analysis (FMEA) to design and CNC programing. "Our constant main topic," says Kempf, "is a setup cost-neutral production, which we handle using TDM." The machines are standing still only for the initial setup of a new part. All other setup processes take place outside of the machines, while the machines do what they were built to do: Machine around the clock.
Production with a System
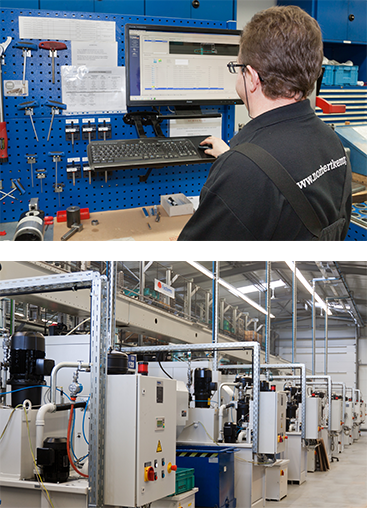
In 2003, Kempf invested in a flexible manufacturing system from the automation specialists Fastems – a machining center with twelve machine pallets. In 2011, the maximum expansion level had been reached but still without upstream tool management. "Then we started the largest project in the company's history – a new production hall, the production system from Fastems MSL/CTS, and the introduction of Tool Data Management, TDM, which supplies both flexible manufacturing systems with tools.
The core of the system is a high rack storage, which houses the machine pallets with the clamping devices and the raw materials. A racking storage and retrieval vehicle transports the pallets to the seven machining centers or to four loading stations for mounting. The central tool storage unit that is arranged at a right angle to this has space for 2500 tools and a crib robot. The steel colleague sorts and puts away new tools and brings worn tools to the withdrawal station. If tools are needed on the machines, it passes them to a gantry robot that travels on rails over to the machine and loads it into its magazine.
The TDM software organizes this complex tool circulation. It is familiar with all of the im-portant tool data, including their remaining tool life. The software keeps track of where each tool is used and where it is located at all times. And as a result, the right tool is available at the right time. The TDM software ensures this by communicating with the control system for the two Fastems production systems, with which it exchanges all necessary data. All processes can be viewed at any time. If something seems to get off course, because for example a tool is missing, the production planners will get informed early enough so that they can then intervene in a timely manner.
Stefan Kempf explains how this works in practice: "We provide each tool with an RFID chip that contains all of the relevant data." Once the tool arrives at the machining center, geometry data and tool life is read. "But above all, the remaining tool life is communicated with used tools." And the system thinks for itself. If a tool receives a tool life warning, the robot delivers a replacement tool into the magazine chain on time.
The Difference between New and Used Tools
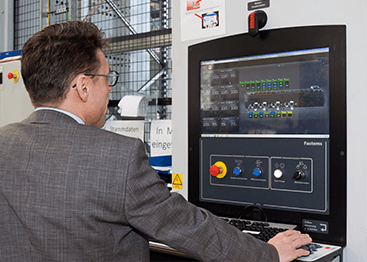
New and refurnished tools have different tool lives – an important information that the system takes into account. At this point, there is no TDM software alternative that can detect up to eight tool states and assign that particular tool. "We know, down to the second, what the tool life of each tool is and how much tool life we need to produce a part. Thirty-six hours in advance, the system executes a resource check to see how much tool life of a tool type is still in the system. If that amount is under the required tool life, our tool assembly area automatically receives an order request and gets informed exactly when the tool will be used."
The TDM software also helps to make sure tools are ready for use. The presetters serve not only the tool assembly. Even more important is a plausibility check that is carried out for each tool installed. The presetters receive up to nine predetermined parameters about the tools from TDM via an interface. These are compared against the actual tool and thus verified. This balance between the actual data and the nominal data stored in TDM ensures that only perfectly mounted tools enter the system. Kempf: "A key issue for reliable production."
Conclusion: At Kempf the focus is on supply security of the machines. TDM reports bottlenecks and problems well in advance so that countermeasures can be taken in a timely manner. The order-oriented tooling and preparation outside of the machines avoids follow-up setup times. Thus, Kempf achieves a nearly 100 percent utilization of his machines despite an average of one new part a day.