Mapping ways to use the tools
A tool can be used in a variety of conditions and with different materials. Mapping this variety as a data record is one of the core functions of the TDM tool management software. After all, TDM is designed to map and manage the tools according to their properties and the parameters that describe them. Above all, assigning several feeds and speeds records with cutting values to one tool assembly enables the user to save their own machining know how. In addition, it reflects the actual use of the tools, which, after all, are often used very variably. "We have customers who have saved hundreds of thousands of euros simply by digitalizing their tool stock and using the correct tool assembly," explained Bernhard Grossmann, member of the engineering department of TDM Systems.
More about the advantages of digitization with TDM
Driven cutting data provides information
Often there are large differences between the target cutting values used during programming and the driven actual values from the machine. Analyzing these and comparing them with the planning data would give big insights in many cases. However, at present there are not yet any solutions and processes on the market that could close this gap. Finally the experts at TDM Systems asked: how can the driven cutting values from the machines be fed back into the NC programming systems?
"We at TDM Systems are aiming to achieve a closed data loop between planning and production. This also includes analyzing the driven cutting data from the machine and comparing it with the planned data. Only in this way can we succeed in improving the NC planning data," explained Grossman. "That's why we took on this issue and developed the TDM Feeds & Speeds Manager together with some customers."
Big Data: Channeling and analyzing data volumes
The driven cutting data from the machine is collected and compressed via middleware. We currently do this using the Comara-Box, a standard industrial PC that's connected to the machine control and communicates with the TDM database server via a web service. A variety of data is recorded, from the beginning of machining to the override settings for speed and feed, feed rate, cutting speeds and duration of tool use. The data is transferred to the TDM Feeds & Speeds Manager and assigned to the machine and the NC program used. In this way, tool by tool, the difference from the planning data can be displayed and analyzed. In the FSM dashboard, the recorded cutting values are visualized and broken down according to different criteria. On the one hand, you get detailed information about the individual machines, starting with the machine utilization, the tool use times, the number of programs and tools, and even the average positions of the feed and speed potentiometers.
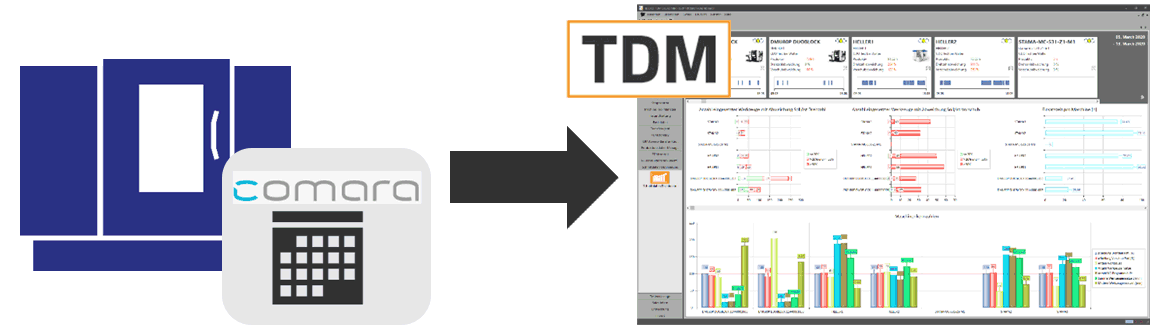
"For the user, it is of particular interest to see the number of tools for which the driven feeds and speeds differ from the planned data," said Bernhard Grossmann. These deviations can be analyzed according to the level of deviation and, for example, the tool uses with the greatest deviations of over 50% can be viewed in detail. The FSM dashboard also provides lots of information about the driven NC programs and how many tools were used.
Secure findings and benefit
Users can also find useful information regarding the length of the machining times. The tools with the longest machining time can be analyzed for each machine. These tools are often the cost drivers in production. FSM therefore also provides users with a solution to identify these. Users can assign all this information to the corresponding tools in the TDM and save it as a feeds and speeds data record. This means the know how is saved and the analyzed cutting data can be planned for the next machining run.
"With the Feeds & Speeds Manager, it is possible, for the first time, to achieve a continuous improvement process for NC programs by evaluating and comparing planned and driven cutting values," said Grossmann. "What really excites me is that we can do this based on a standard solution." This enables permanent optimization of NC planning data and therefore a reduction in machine down time, extensive time savings and increased product quality thanks to verified data. If the TDM Integrated NC-Program Manager is also used, users obtain seamless statistics regarding which NC program was run on which machine and how often.
For whom is FSM of interest?
The Feeds & Speeds Manager is primarily of interest to contract and single part manufacturers, but also to companies that machine small batches and therefore cannot run any trial machining. The more difficult the materials to be machined, the greater the potential for optimization thanks to FSM.