Reproducibility as a guarantee of quality
To manufacture our filigree metal parts which, together with the quartz and crystal, form the heart of our sensors, Kistler runs a workshop with around 30 employees at their headquarters in Winterthur. The high-quality requirements place great demands on precision and on the materials that are to be processed. To manufacture the extremely small metal parts, we take a cautious approach to the physical limits at all times. To be able to meet the requirements in the long term and guarantee the reproducibility, all relevant information must be saved. For this reason, the company sought a tool management software that would also allow all required items to be managed at the same time.
KETA: A strong partner from Switzerland who adapts the software to our requirements and conditions
We found what we were looking for with the Tool Data Management from TDM Systems GmbH and the local sales partner KETA Engineering. In an initial step, the exact system requirements and processes in the tool environment were analyzed and retained in a solution concept. KETA Engineering was able to offer their experience of over 20 years to this, meaning that the existing environment of cabinet systems could be seamlessly integrated into the new software.
The software was installed in October 2016 and, once the data is processed and transferred from the old system, was successfully operated. The transfer of the revised and standardized legacy data had the advantage that the correct data was available in the system right from the beginning. This led to a fast production start.
Since then, the complete tool flow, including the stock management and the restocking of tool items and measuring and inspection equipment, is maintained centrally in the TDM tool management.
The intelligent cabinet software from TDM is also used for simple and monitored tool dispensing on the ToolBox tool cabinets from Brütsch Rüegger around the clock.
A wide variety of tool items with small dimensions led to a large number of stock locations in the TDM Tool Crib Module. In total, over 40,000 locations are managed in the crib organization, which are automatically controlled for the removal and storage. It was possible to successfully implement all requirements from the analysis phase using optimum system parametrization and technical support.
Project support
Important key factors for successfully implementing a project include sound and realistic planning, the inclusion of all involved persons right from the start of the project, and expert support from the specialists and suppliers. During the course of the project, KETA Engineering was always ready to provide assistance and advice. Experience from other projects was also taken into account right from the beginning. Any problems and ambiguities could be solved easily and in good time thanks to close collaboration, meaning that the project could be completed on time.
Tool provision in accordance with SMED
At the separate setup workstation, all production orders are prepared. This reduces machine downtimes to a minimum. All of the items that are required for the setup process are stored in the ToolBox cabinets.
At the setup workstation, an employee assembles the items to create a tool assembly. The drawing-compliant assembly is displayed and guaranteed by TDM. The tools are then calibrated using a CNC presetting device. This also obtains the information from TDM and transmits the data directly and digitally to the machines. Thanks to the continuous data flow, all media incompatibilities can be excluded. Furthermore, this ensures that the same tools and cutting geometries, including the optimum feeds & speeds, are always used. This leads to a high level of reproducibility and a consistently high level of quality, and it excludes sources of error. The large range of parts constantly demands new tool items. To date, a total of over 1000 tool assemblies have been created from the master data for around 5000 individual tool items.
From digitalization to networked production
Thanks to the centralized stock management, on-time purchase requests can now be automatically reported to the ERP system, which triggers automatically a purchasing request and, as a result, guarantees a high level of availability of the tool items. Time-consuming, manual recording of tool procurement could therefore be eliminated.
A wide range of specialand hand-made tools were recorded and standardized. In addition to the features such as classification, geometry and technology, corresponding 3D tool models were also created. The focus of this work is that no standalone solutions are created and the data can be re-used in all of the surrounding systems. In parallel to the TDM implementation, a new presetter was also set-up and integrated. The project moves forward with the evaluation of CAM software. All connections obtain the data from the same central TDM database, which hereby supports all of the manufacturing-relevant sub-processes as an integrated database.
Database for realistic CAM programming
The more accurately the items are recorded and modeled, the more precisely they can be simulated in the CAM system. This information is essential if you want the collision monitoring to be carried out realistically. Here too, TDM forms the database and provides the 3D tool model for the respective CAM and NC simulation system. Thanks to the deep level of integration of the CAM programming, presetting device, automatic tool crib and the machines, TDM could be used to implement comprehensive Tool Lifecycle Management.
Overall benefits for Kistler Instrumente AG
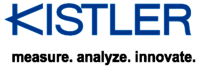
All in all, for our workshop, the TDM software is not only a tool for carrying out stock management or operating the ToolBox. Rather, it is the central database for a long-term increase in productivity. Whether this involves the assembly instructions for the tool assembly, presetting the machine‘s geometry data or the simulation in CAM software. Last but not least, the TDM software also leads to a smaller and more suitable standard range, which leads to a reduction in stock. At the same time, we can exchange our information with the sites across the world.